The "Pioneer machine" at the C.C. Stern Type Foundry. (Named after the job shop where this Linotype Model 31 originated) It's a workhorse, and makes some mighty fine slugs. You can tell that it is a workhorse by all of that paper attached to it. Oh, also there's a reminder that the thermometer is still in the pot, so don't go pulling the clutch just yet.
Coaxing machines out of hibernation at the C.C. Stern Type Foundry
Now that they are well acclimated to the new space, we're coaxing the machines back to life. We're quite pleased with the VFDs (used for 3 phase conversion). So far so good. We chose the WEG-CFW300 VFD, which seems to be a no-frills unit with a relatively user friendly display.
Machine adjustment notes
Problem: border slide block would not cast
Fix: Left and Right vise were slightly out of adjustment when 30 em line was set. At the 30 em setting, the locking block on the adjusting rod was set so that there was excessive space between border matrix slide block and vise which caused the pump stop to activate when attempting casting. Both left and right vise jaws were adjusted, as well as the em scale guide on the adjusting bar.
Comments: There is a wicked looking brazing repair towards the back of the vise closing lever. At some point in this machine’s history, something caused the lever to crack, or perhaps entirely break off. I'm guessing this happened while Don White was operating this machine in his shop under the Morrision bridge years ago. He loved this machine. As I recall, I believe that Don was the original owner, which is a big deal for a small job shop back in the day. I can only imagine that Don’s heart hit the floor right along with the thud of this heavy cast iron lever if that break happened while he was behind the keyboard.
When you see repairs on the machine like this, it sends up the red flags - perhaps this is why the machine is slightly out of adjustment? To prevent what ever caused this break to reoccur? Or did it happen when the vise was lowered to the second position? Just something to ponder before pulling out the wrenches and making bold adjustments. Incremental is the key, and take it slow.
I was happy to (re)discover that the left vise jaw wedge is spring activated, not cam driven, so it gave me a little more confidence that at least the left jaw adjustment wouldn't cause a nasty lever-breaking jam. But again, take it slow, bro. Discovering that spring mechanism was another moment to bow down to the Mergenthaler crew. These engineering features offer yet another a glimpse into the brilliance of Ottmar and his team.
Note to self: Those felts along the left vise jaw wedge need some love.
Following the maintenance steps on page 131, chapter 11 in Linotype Machine Principles, the adjustments were successfully completed, and in the process I ended up with a partial galley of decorative border. Not a bad work day at the C.C. Stern Type Foundry.
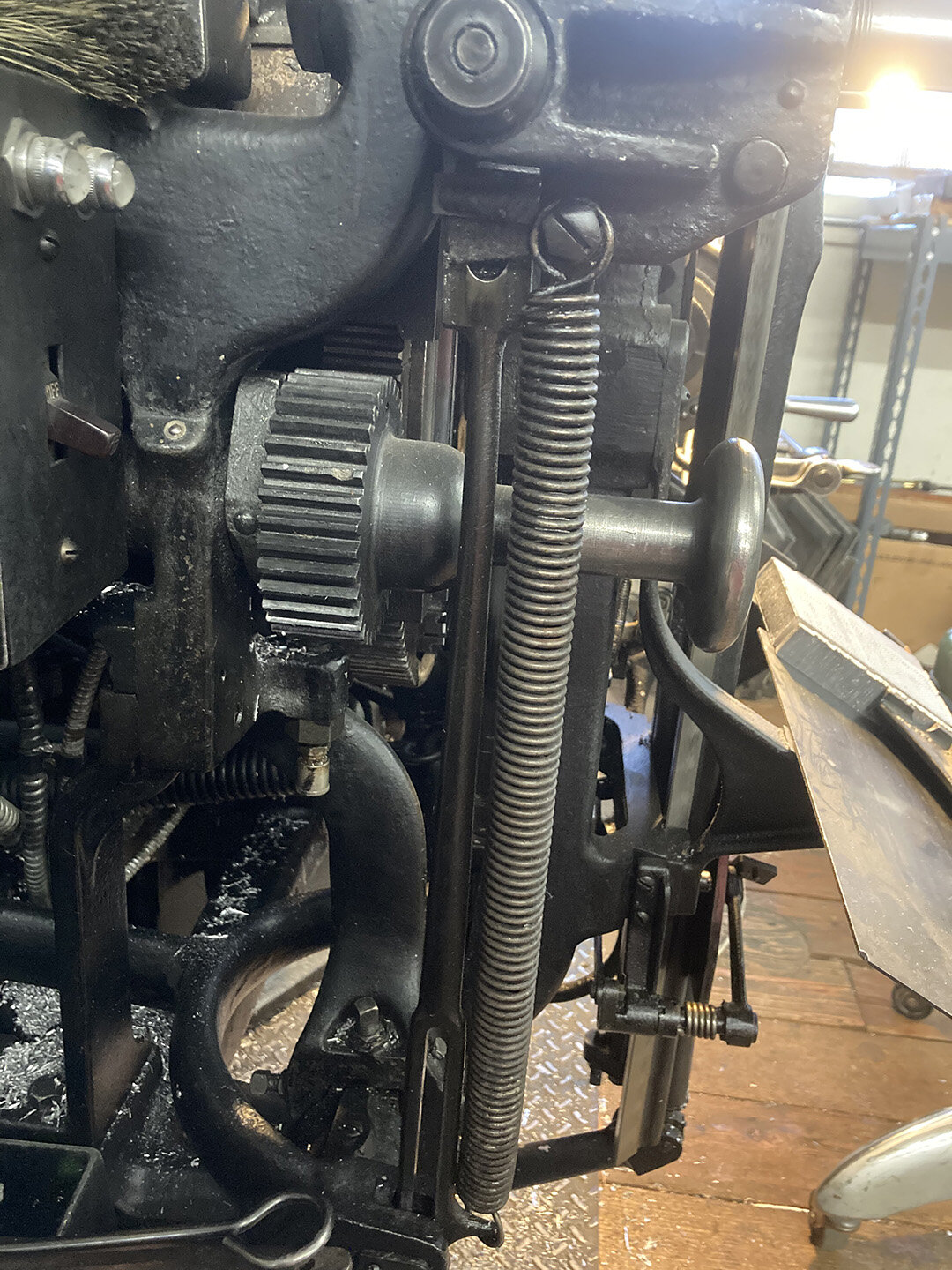
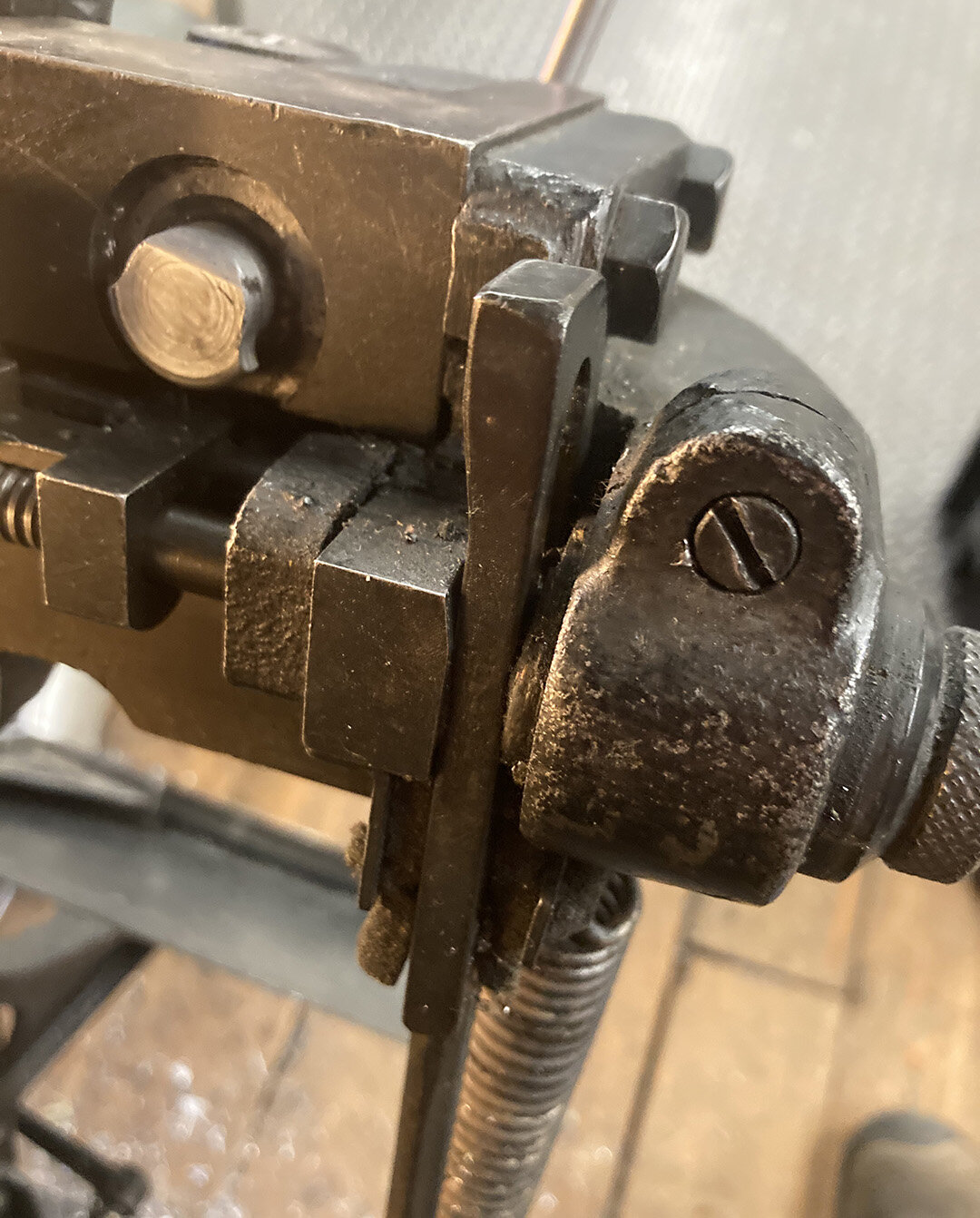
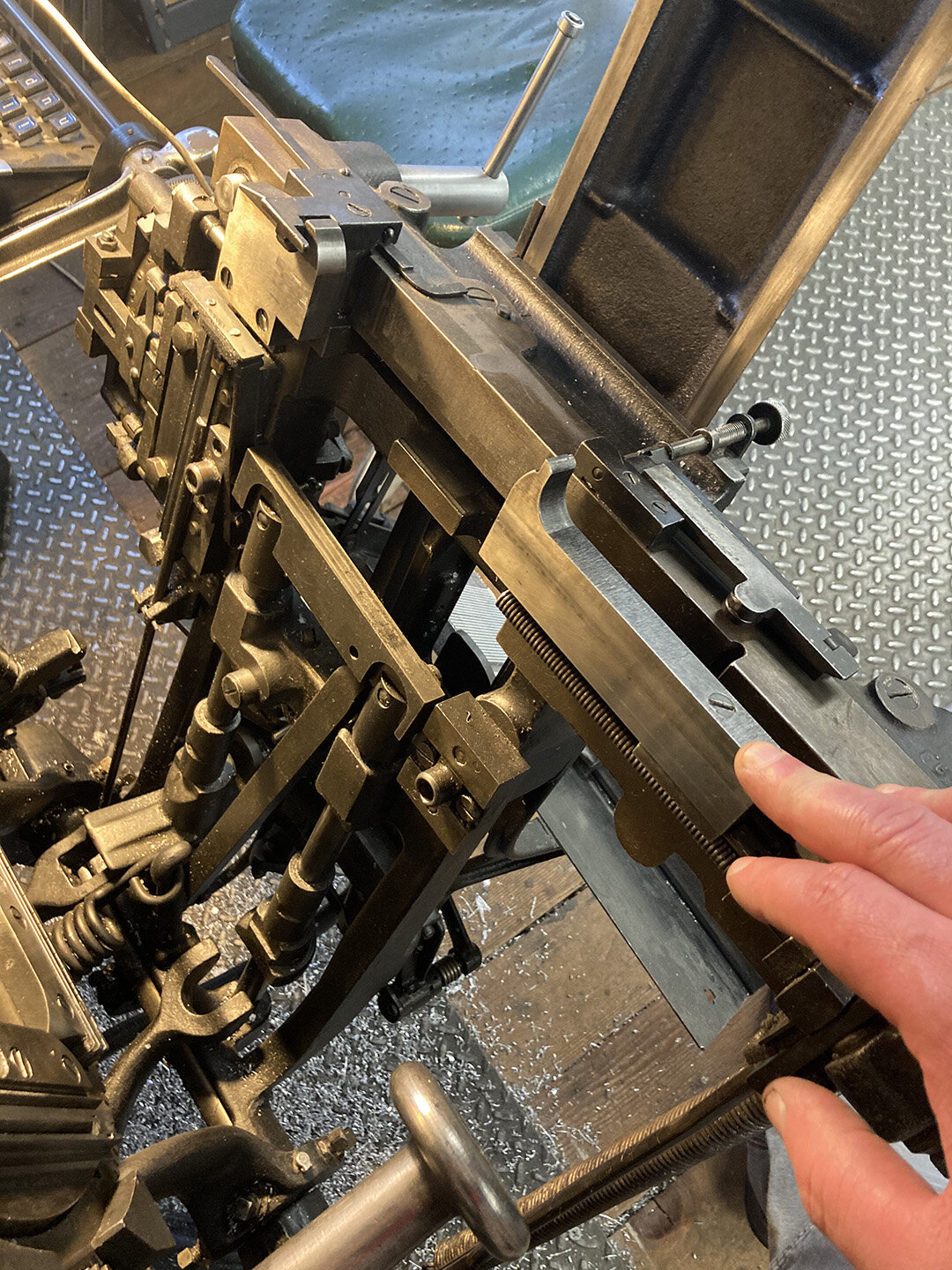
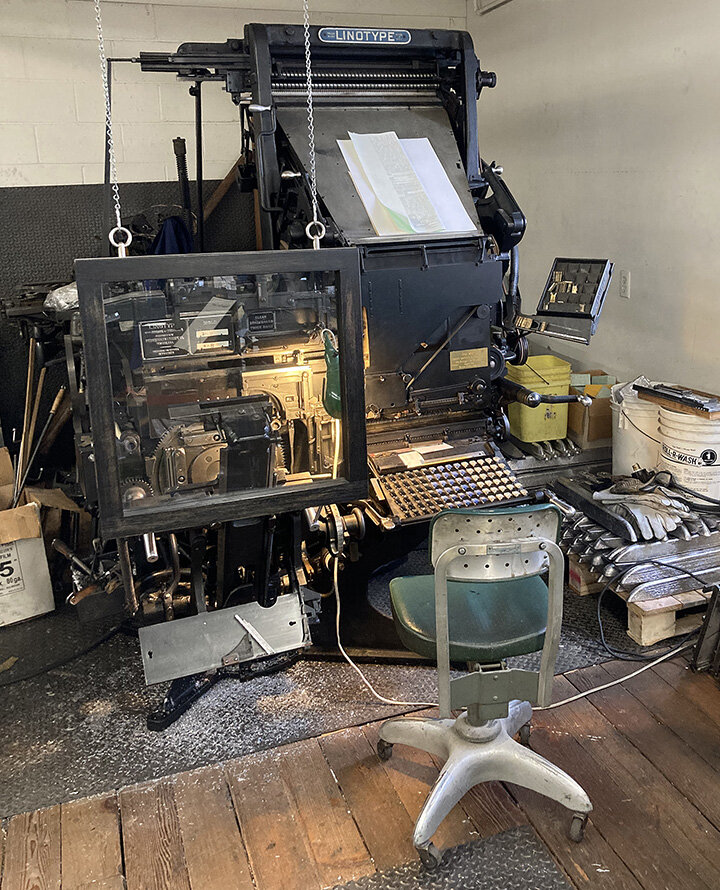
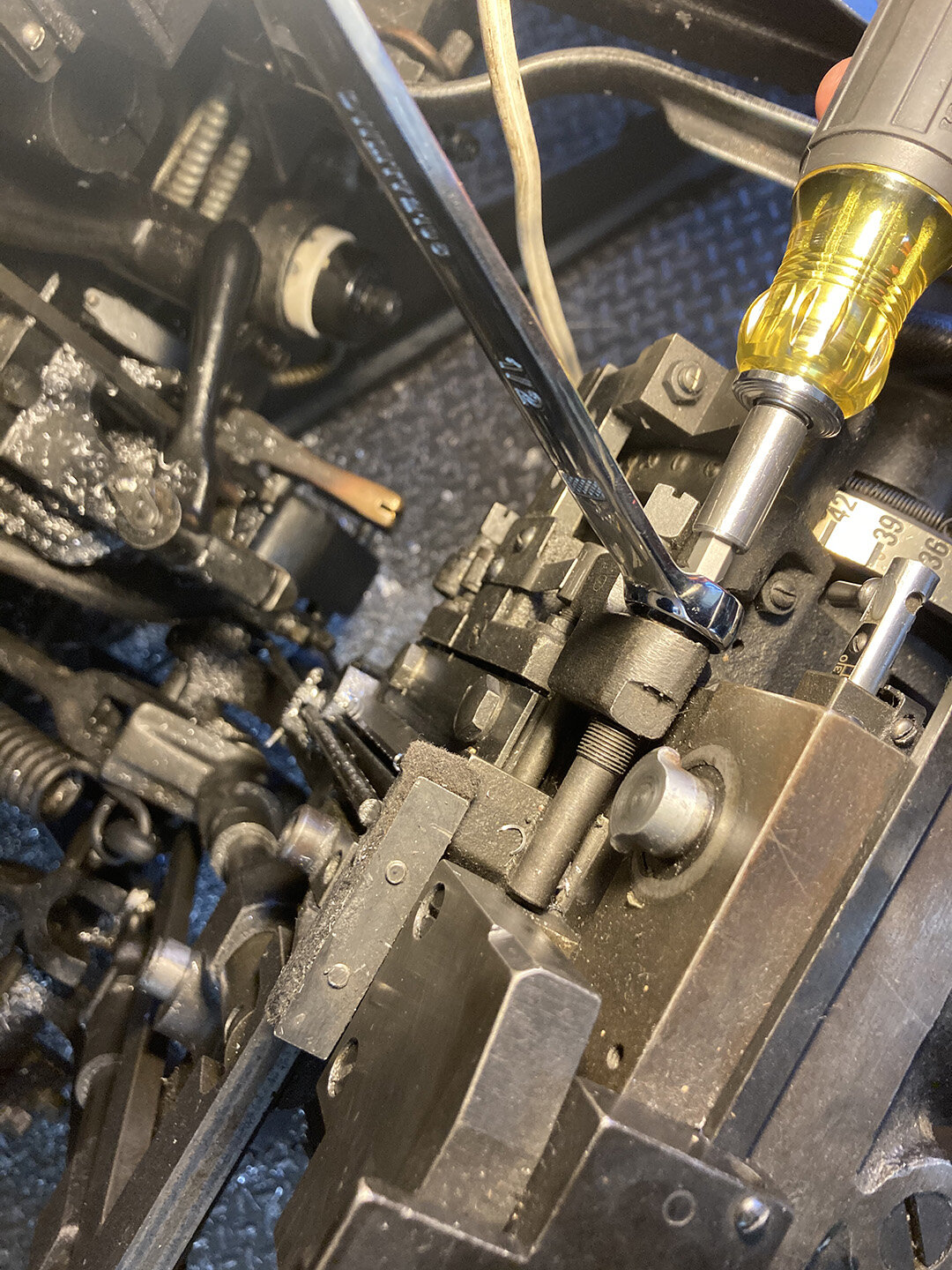
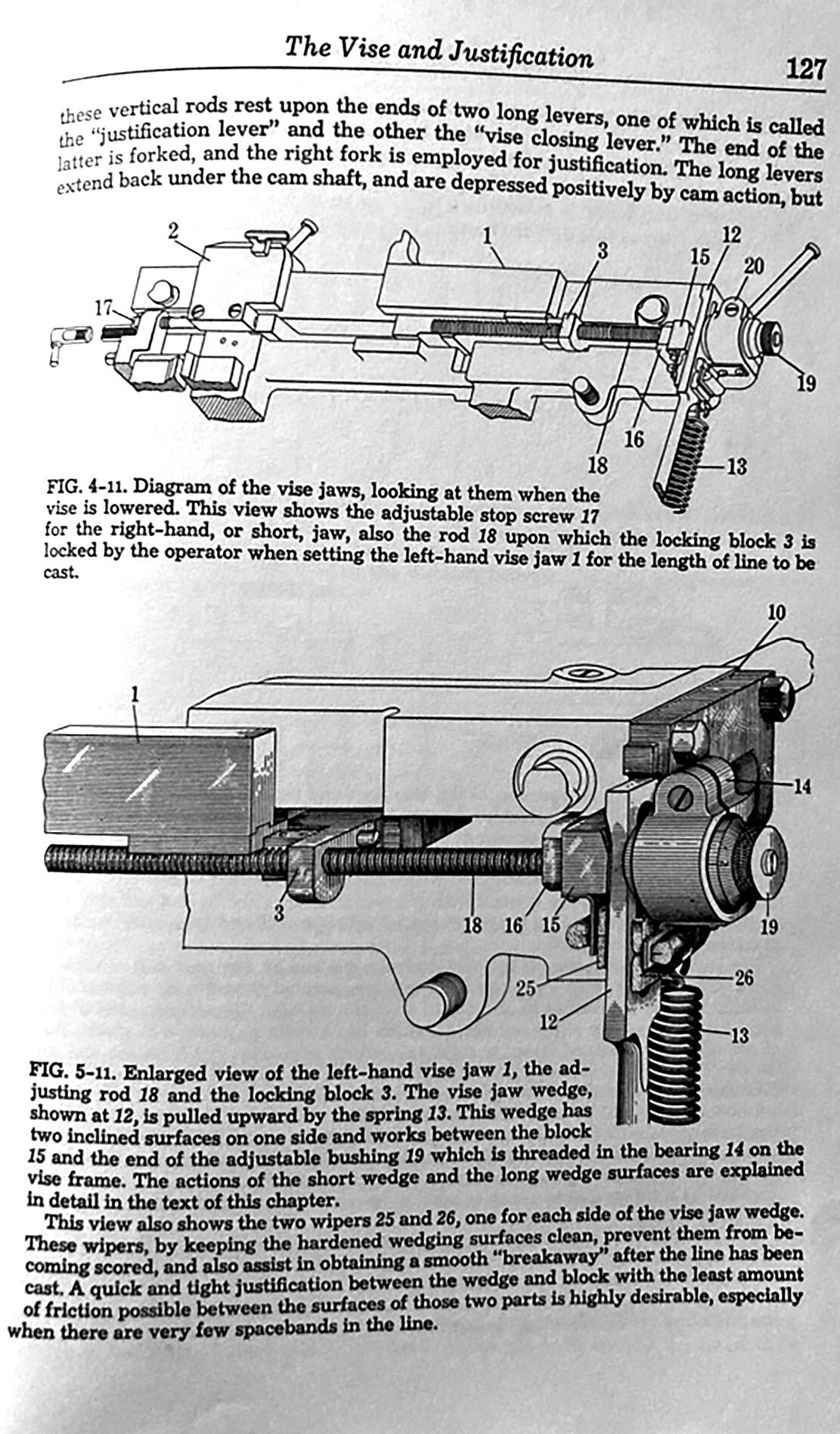
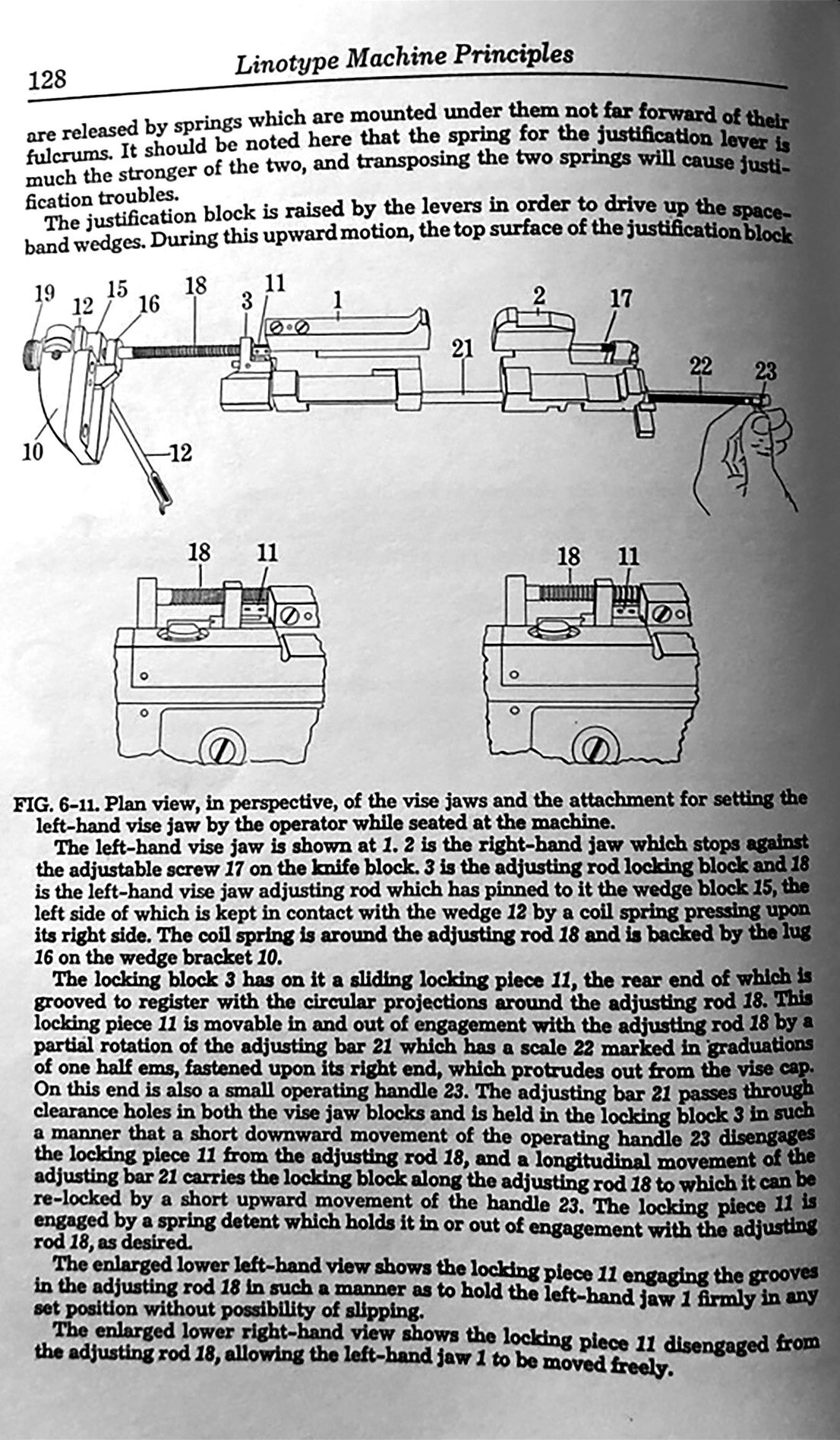
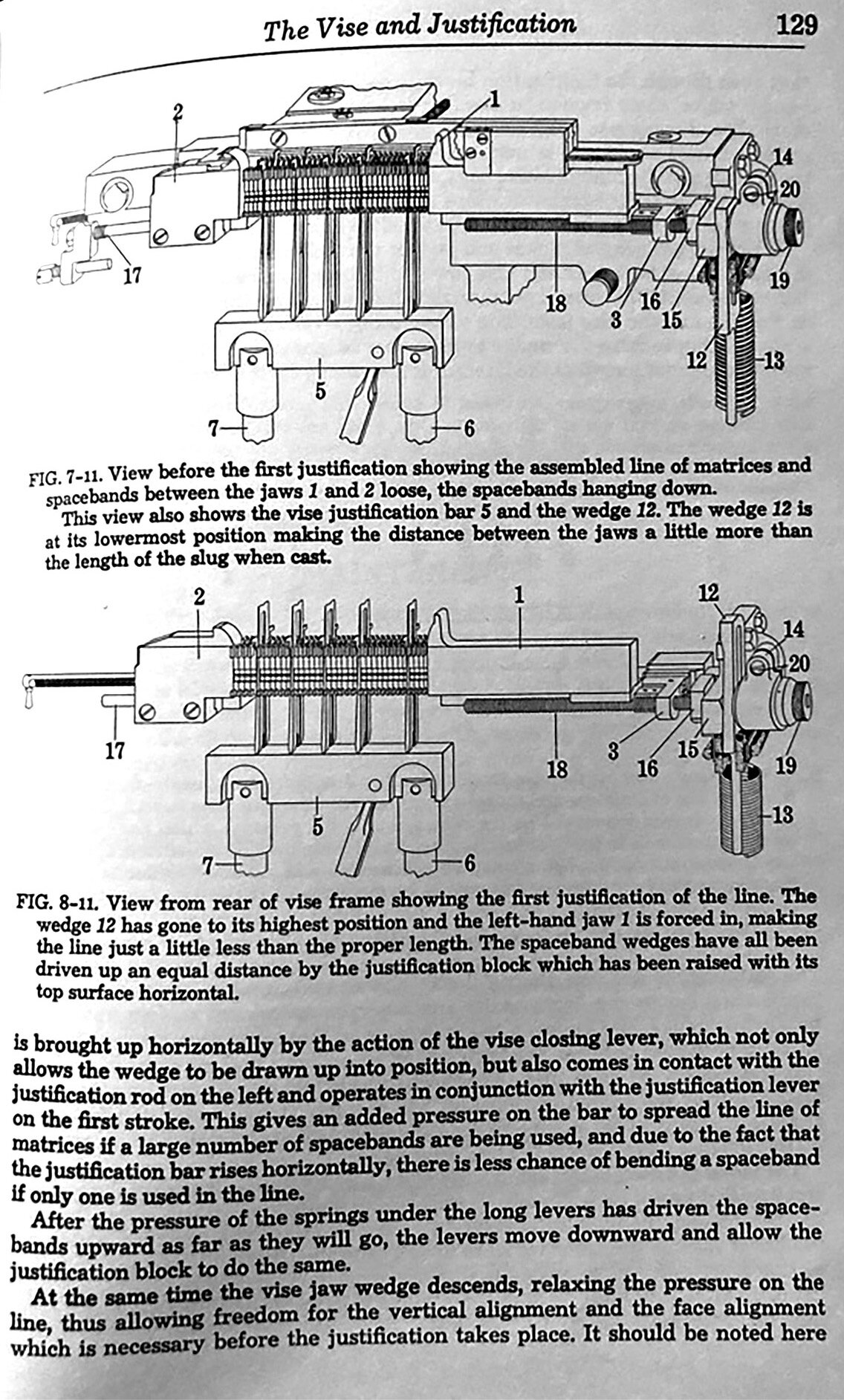
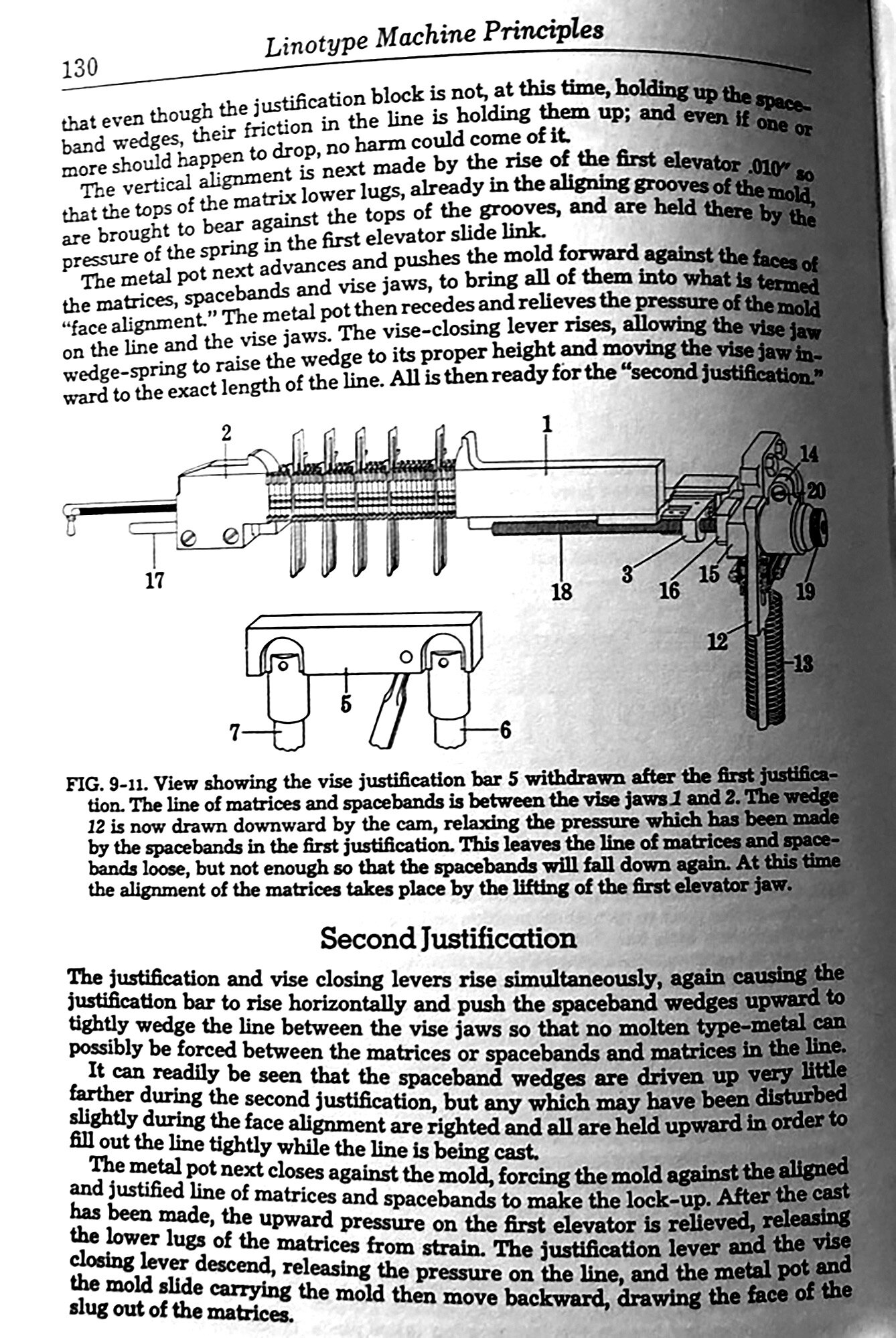
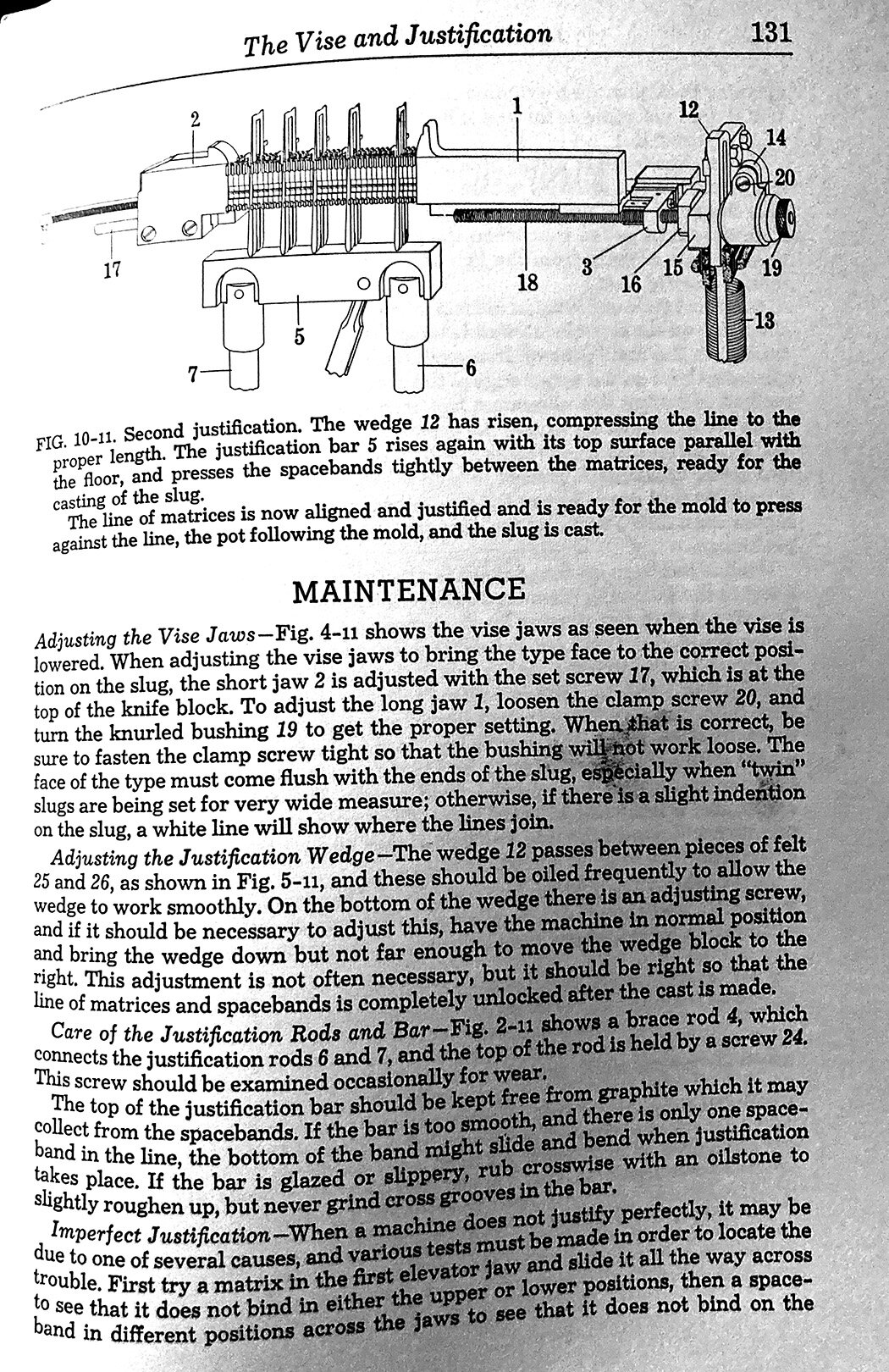
Space Band box needs some attention
I took this pic while at the C.C. Stern Type Foundry board members’ work session. Chris Chen was in town, so the focus was on the comp caster. Exciting stuff was happening over there at the comp machine, but too many board members around the type metal spoils the alloy. Or at least that was my theory that day. So Linotype house cleaning was my strategy. Number 4 spacebands have occasionally been hanging up at the top of the box and not sliding into place. After some cleaning and an added shim, the choke point was alleviated. Not entirely fixed, but certainly an improvement.
Alumilite Pi
Linotype Alumilite Magazines Shall not be trusted. This is the second one that has failed on me. No fun. The brass bottom magazines are quite heavy to haul around, but those suckers are solid. I haven't experienced this issue with the heavier magazines.
Linomite
I noticed a slight little build up of type metal on the pump plunger rod when I started casting this evening, and after a couple hours of casting lines this is what that build up became:
Linomite! It was enough to restrict the plunger from returning to its fullest upward position. Gotta keep an eye on this next time. I'm guessing that this happened because the pot was a bit too cool. I'll test the theory next time we cast. Otherwise, anyone out there have tips on how to prevent this?
The properly justified slug
Got it! The properly justified slug
Resilient Mold Cam Adjustment
Resilient Mold Cam Adjustment
Teachers
Consulting with the teachers
Handy Illustration of First-Elevator Cam
This illustration is a useful reference if you are in the back of the machine and cycling it by hand, and you need to know when to stop cycling(!) By looking at this cam, you can determine when the first elevator is resting on the vise cap, or when the justifications take place, etc. This illustration is scanned from the Intertype Book of Instruction, page 46.
Release the pressure of pot lever spring
Still trouble shooting - But first! Release the pressure of pot lever spring!
Testing proper clearance between the face of the mold and vise jaws
Still Trouble Shooting. Testing proper clearance between the face of the mold and vise jaws
Page 150
Hydraquadder causing the problem?
Trouble shooting....
The Trouble Line
Occasionally while running the machine, I've experienced a "no cast". This happened randomly, or at least it seemed to be random, because after a second attempt to cast the same line often the machine would give in and produce the slug. When it didn't cast a second time, I would switch it up slightly and maybe add a thin space, etc. and I could get it to go. It didn't happen frequently enough for me to explore the issue until recently. The line pictured above is the one that stopped me and got me to look into the problem.
In this case I was setting 10pt on 10pt mold, 18 pica width, first position. I was using standard justification with the hydraquadder off. As you can see, it's a full line, 6 space bands with less than a pica to go. I sent the same line through as it is pictured (but recreated with different matrices) several times. No go. Other lines that seemed to be similar length and spacing did go, so it was a mystery to me why this one would not.
More details to come....
Linotype Drive Belt
I'm in the process of tracking down belt material for the main drive belt. I stopped in on our local supplier Empire Rubber where the crew there presented me with a bunch of great info and options. Good guys and a good resource. With their help, I should be able to match the lacing and material.
Update:
The belt that I ended up using was:
Empire Rubber's item number: 20045012
Description: 4/140 II Tan FSxFS 1.5" W
Flexco Clipper Lace was used, added to trim length of 79.5"
Identifying Linotype Spacebands
The spacebands that I have here at the shop are 4 lines. I assumed that the number of identifying lines marked in the side of the spaceband correspond with the thickness of the space. Nope. I was wrong. The breakdown is below. Info from "Linotype Keyboard Operation" book.
One Line: Thick
Minimum .0375
Maximum .1035
For Normal spacing of medium size faces where close spacing is not required.
Two Lines: Extra Thin
Minimum .028
Maximum .0943
For close spacing. Recommended for offices doing good book and job work and those using small faces.
Three Lines: Extra Thick
Minimum .046
Maximum .146
Used only for large display faces where wide spacing is required.
Four Lines: Special Taper
Minimum .0369
Maximum .1219
Similar to the wide range (see below) but a little thicker at both minimum and maximum points.
Five Lines: Wide Range
Minimum .0345
Maximum .1194
Gives extreme flexibility of spacing. Thin enough for close spacing, with ample range of expansion for wide spacing.
Trust the spacebands....
Below is a scan of a proof of some lines cast this past weekend for a friend. 8pt Linotype Paragon set on 23 pica line, regular justification. I let the space bands do their work, and wanted to learn their tolerances and get used to how a line would space out according to how many spaces bands were used vs. word size, etc. I figured this face could handle some "gappy" word spaces, but I was surprised at how this composition appears fairly consistent. Even though there are some lines with ambitious word spacing, none of them stand out as being too obnoxious with noticeable "holes" or "rivers" in the composition.
What I learned: generally speaking, space bands have a "spread" of 3 pts, so if you have at least 5 space bands in a line, they will easily take up a pica worth of space. I'll add a separate post which will describe the markings and different thickness of Linotype spacebands.
Another thing I was reminded of after setting these lines are the rules for indentation. For commercial work, the rule of thumb is to indent paragraphs by an em for lines set up to 20 picas. 1.5 ems for lines up to 25 picas, and 2 ems for lines above 25 picas. Of course depending on type size, leading, etc. there are exceptions. But after looking at the paragraphs I set below, I think my 2 em indentations are a bit too aggressive. I referenced the book "Linotype Keyboard Operation" for the refresher.
Oh, after clicking on this photo to take a closer look, I noticed something else. See the lower case "i" with a problem? I'll have to run the mats out and have a look at them.
Mold 10-18 F7660
Couple stupid things I did while casting this evening:
1. Fired up the machine after a long day of regular job printing. (Not the best idea to attempt to cast while not quite on the ball.)
2. Attempted to cast the second position of a 14 pt (regular 2 letter) matrices using a 10-18 F7660 mold.
3. Tried it again.
4. Wondered why the machine was squirting.
Lesson (note to self): Don't do that. First position is no problem but second will not work. Check positioning of mat on mold before attempting to cast. And, do a little research on this particular mold: Mold 10-18 F7660.
Additional thoughts on delivery and elevator transfer cam damage.
Thinking more on Keelan’s damaged delivery and elevator transfer cam. Bill Spurling pointed out this repair that had been made on his Model 14
I know brazing cast iron can be tricky business, and it seems to be difficult to find folks who are willing to do it these days, but it can be done and in this case it is a clean effective repair. This solution seems to be a heck of a lot simpler than pulling the main cams and shaft apart. Still, the mystery is: how did this thing break? As far as I can see, this part of the cam is used to assist in retracting the ejector lever after the slug is ejected, but it seems that the mold cam lever does most of this work. I can't really imagine what would have caused this much force to crack the cam.
The Linotype Machine that makes the Fiddleink
This is my machine, a Linotype Model 31. The photo below is taken at its original location: the former Pioneer Printing Company in Vancouver, Washington. It is now located at my workplace, Stumptown Printers.
Pioneer Printing was the original and only owner until we purchased it, and I do believe that the machine was moved only once over the 64 years that they owned it.
The machine is a single distributor 1946 Linotype 31 “4 pocket” mold with hydraquadder. Serial Number 57557. A friend of ours remembers staring into this plate glass window as a kid, transfixed by the sound of the presses, the scent of ink and the movement of this gentle giant with its slow rolling oversized cams. These memories are what inspired him to pursue a career in printing. He's retired now, and I haven't actually told him that the machine is now on our floor. I wonder if he would be excited to see it again, or if he would want to run for the hills at the sight of it. It’s hard to say.
The folks at Pioneer Printing were able to give me a copy of the original “bill of sale with mortgage” issued by the Mergenthaler Linotype Company. The purchase price of this particular machine in 1946 was $6843.00. That’s some serious coin for that time. It's equal to about $75,000 by today’s dollar value. We saved it from the scrap yard for 3 Ben Franklins, a promise to take good care of it and for the cost of rigging. However, considering that the cost of brass is higher these days than it has been for years, and that the metal value alone is often higher than what print nerds like myself can afford to shell out, I feel like the previous owners were generous for allowing us to “save” the machine instead of simply scrapping the machine.
Promotional piece from Pioneer Printing, 11 years before this Linotype was built!